Written By: Mike Ingram, President & CEO
Do you know why you need to know how much fuel your aircraft is consuming at any given time? Ok, there are some obvious reasons, like to know that the fuel is being consumed by the engine. If there is fuel flowing, then there is a really good chance that your engine is operating, no fuel flow no engine power…that’s not good. Other reasons include using it for your fuel totalizer, predictions, fuel range rings, and engine leaning. Since Shadin is in the business of making fuel flow transducers, it is important to know the value my product provides to my customers.
A fuel totalizer is an estimated fuel quantity based on the pilot’s entry of how much fuel is on board. When the pilot fires up their Avidyne Entegra or Garmin G1000, the first screen is a Fuel Entry page. This page enables a pilot to add how much fuel was added to the airplane, and at least on the Avidyne’s, it allowed “Fuel to Full”, “Fuel to Tabs”, and a manual entry. After confirming the amount of fuel on board, the system uses this amount as the starting point for fuel quantity and any fuel predictions based on the fuel flow. Why doesn’t the system use fuel quantity? Well, the fuel quantity from the fuel tanks is too grossly measured, and definitely cannot be used to accurately predict fuel remaining values.
As an example, at power on, if the pilot indicates full fuel with a 50 Gallon tank, and then takes-off. When flying, the fuel flow is showing 20 Gallons per Hour, then the total fuel duration on board is 2.5 hours – pretty simple math. When there is a loaded flight plan, there will be ‘fuel remaining’ at each waypoint to help the pilot know the fuel amount along his/her trip. When the throttle is adjusted then the fuel remaining amounts will fluctuate as well.
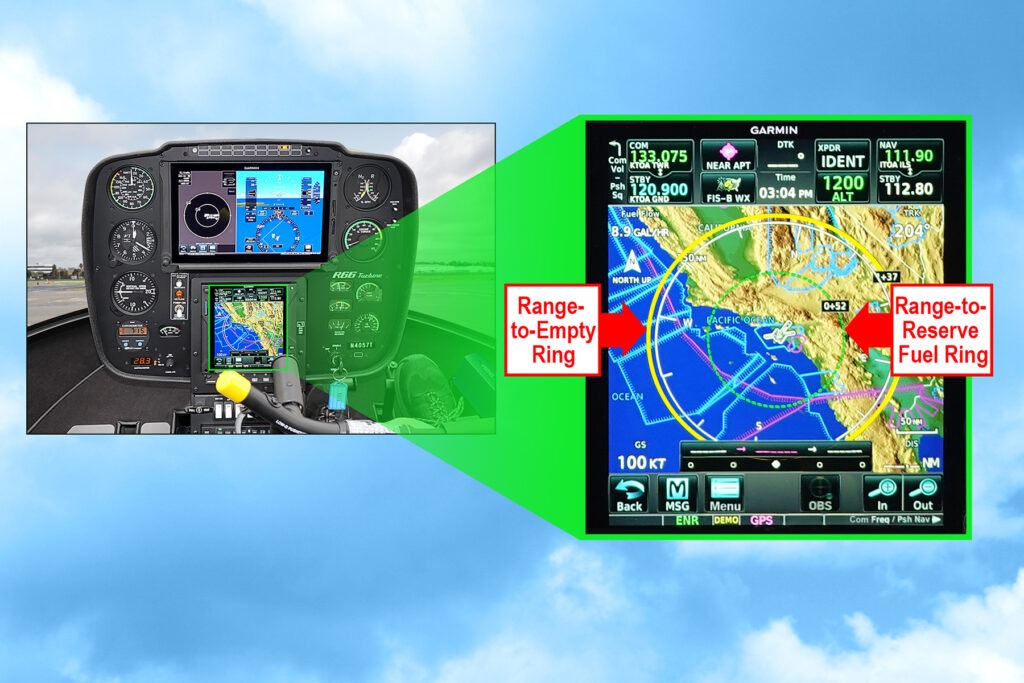
On the Garmin GTN’s, they have created a visual range ring for how far the aircraft can fly with the fuel on board cruising at a specific fuel flow. The Shadin fuel flow transducer outputs pulses at a certain count per gallon, or k-factor, and your avionics converts it to Gallons or Pounds per hour. Fuel flow transducers either come standard, added as an option, or can be retrofitted onto you aircraft or helicopter (Robinson R66 above) so that the pilot’s can have this slick fuel range ring function.
Engine leaning while monitoring the fuel flow also enables a safer means of flying your small airplane in a state of ‘Best Economy’ or ‘Best Power’. The process of engine leaning in a Cirrus is simplified by an Avidyne function called “Lean Assist”. This algorithm on the Avidyne EX5000 MFD, allows the pilot to more easily fly with engine temperatures and fuel consumption at optimum levels. Watch the YouTube video to see it in action, https://www.youtube.com/watch?v=zIWCd-7T0DQ. Lean Assist is close-to-my-heart since it was one of my patents at Avidyne and it was so much fun researching, designing, and flight testing. If you want to read how a lawyer can butcher a good engineering white paper, go to https://patents.google.com/patent/US20050137778.
Before I get into the details, engine leaning is reducing the fuel to air ratio in a piston engine. There is a leaning ‘knob’ that is pulled by the pilot to reduce the fuel to the engine, or pushed full in to make the mixture most rich. As the altitude increases, the density of air decreases, so the amount of fuel to air will also need to be reduced by the pilot, or the engine will be ‘flooded’.
When leaning your engine for the best fuel economy, you will either follow the Avidyne instructions or do these easy steps. First put the aircraft in cruise at a straight-and-level attitude, with a constant power (RPM and MAP). Start pulling your mixture knob, slowly, while watching your exhaust gas temperatures (EGTs), your Cylinder Head Temperatures (CHTs), and your Fuel Flow. As you reduce your fuel (pulling your mixture knob), the EGTs will rise together. The EGTs are measuring the temperatures of the air and smoke in the exhaust pipes just beyond the cylinder firing. The CHTs are measuring the temperatures of the cylinder block or metal, which will take longer than the EGTs to rise. Keep reducing your fuel and at some point they will start to peak and then go down, this is putting the engine in a ‘lean of peak’ mode. When the EGTs are between 25F and 50F below peak, then stop reducing your fuel mixture. You don’t want to starve your engine of fuel by pulling back too much on the fuel. And also watch the CHTs to make sure you’re not going into the yellow or red ranges. BIG WARNING: Make sure you check your engine specifications before doing this!!
When leaning your engine for Best Power, start your leaning process the same way. When your EGTs hit their peaks, then increase the fuel mixture (push knob in a little bit). You will see the EGTs reduce and typically if you are 50F to 100F below peak and on the Rich-side of peak, then you are in a Best Power state, which is most optimally running your engine at its highest percentage power for the throttle setting. Yes, you will use more fuel, and you may or may not be going any faster than being in Best Economy. I’ve seen a few knots of higher speed with flying Best Power vs. Best Economy, so I like fly in Best Economy. It is pilot preference, and there are many emotional opinions on both sides of the ‘peaks’.
You’ve finally reached the end and hopefully I’ve convinced you why you need fuel flow. Here is my subtle sales pitch, Shadin Avionics makes the best fuel flow transducers and systems on the planet. Contact Ken (ken.pearson@shadin.com) or Trevor (tlund@shadin.com) to learn more, or to submit your order!